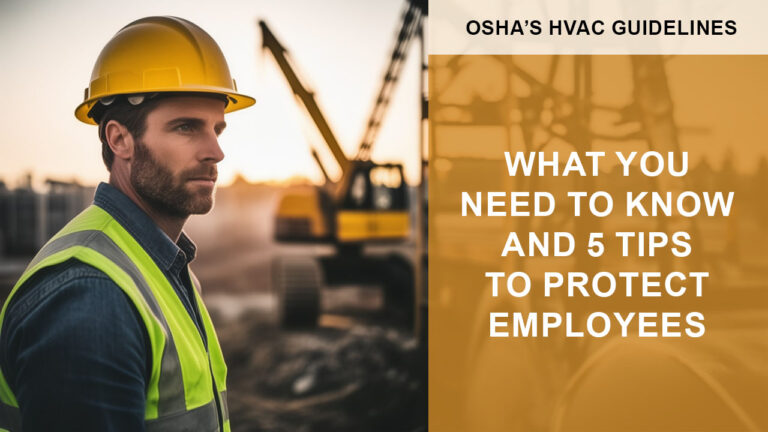
Table of Contents
OSHA (Occupational Safety And Health Administration) has many safety guidelines and rules. According to government research, OSHA has prevented more than 60% of workplace injuries since 1971—when President Nixon officially commissioned OSHA at the time.
Since then, OSHA has found loopholes in the security and safety of specific industries, like general, construction, maritime, and agriculture industries. And now they focus on ensuring safety in workplaces through specific courses like OSHA 10- and 30-hour training.
But, one area where OSHA safety tips mainly come in handy is refrigerants or any subzero working environments. In the last year, there were around 2400 reported incidents in this particular niche. So, let’s find out how you can protect your team in such an environment.
What are OSHA HVAC Guidelines For Refrigerant Safety
One of the primary concerns of anyone working in refrigerant or sub-zero areas is oxygen. That’s because the air in closed refrigerated space is usually heavier, and it’s not exactly easy to breathe. But, besides fatal freezing, there are a ton of other possible hazards in such environments too.
That’s why OSHA safety tips for workplaces focus particularly on refrigeration and require workplaces to abide by a few critical laws. These regulations put forward by OSHA include:
- Ensure proper training for all personnel handling refrigerants.
- Implement regular equipment maintenance procedures.
- Monitor and address refrigerant leaks promptly.
- Provide adequate ventilation in areas where refrigerants are used.
- Use proper personal protective equipment (PPE).
- Establish emergency response procedures for refrigerant leaks or spills.
- Follow the manufacturer’s instructions for handling and storing refrigerants.
- Label refrigerant containers properly.
- Conduct regular inspections of refrigeration systems.
- Train employees on emergency shutdown procedures.
- Properly dispose of refrigerants according to regulations.
- Keep accurate records of refrigerant usage and maintenance activities.
These guidelines and OSHA office safety tips ensure that workers and supervisors stay safe while working in such environments. However, there are constant upgrades and changes to some guidelines, so it’s essential to keep an eye on that too.
Why Are OSHA HVAC Guidelines For Refrigerant Safety Important?
HVAC guidelines protect workers from a lot of different hazards and protect a workplace from falling into any sort of PR nightmare. That’s why these guidelines are essential to secure the workplace from any such dire scenario.
As discussed before, one of the critical areas that HVAC guidelines cover is refrigerant safety. It doesn’t only cover all the key areas but also provides directives in specific situations. That’s why, it’s essential that companies abide by these guidelines, as they are essential for:
- Prevents exposure to harmful refrigerant chemicals;
- Reduces the risk of leaks and accidents;
- Ensures proper handling and storage procedures;
- Protects workers from health hazards and injuries;
- And promotes environmental responsibility and sustainability.
That’s why these guidelines are important as it focuses on all of the key necessities to prevent accidents in a subzero working environment. Besides that, refrigerants require thorough maintenance and updates. These guidelines focus on ensuring those.
5 Key Tactics To Protect Your Team From Refrigerant Hazards
There are a few tactics that are necessary, not only because they’re the right thing to do but also because OSHA regulates these tactics.
So, here are the five key tactics that can help supervisors or employers protect their workers:
1: Proper Training and Education
Proper training and education are a necessity in ensuring any workplace’s safety. It’s no different for preventing refrigerant hazards, and some might even argue that it’s more important than ordinary workplaces. That’s why it’s essential to provide workers and supervisors in such places with training.
That’s why every employer should regulate OSHA 30 and OSHA 30-hour training programs. The more the workers and supervisors know about safety, the better they will be prepared to tackle such issues.
2: Regular Maintenance and Inspections
Regular maintenance and inspections of refrigerated areas are necessary. Usually, these refrigerated areas are accompanied by gasses and other elements that provide the cold climate with the elements necessary.
So, any sort of leak or damage can be fatal. That’s why it’s important to fix such issues and comply with welding safety tips OSHA provides while doing so. It won’t only protect the employees, but also prevent damaging risk to any of the expensive equipment or devices.
3: Use of Personal Protective Equipment (PPE)
Personal Protective Equipment or PPE is a necessary element in any sort of personal training. The use of said equipment is regulated in most workplaces that fall under OSHA’s big four, aka general, construction, agriculture, and maritime.
However, in refrigeration-based workplaces, personal protective equipment might include:
- Nitrite gloves;
- Face/breathing masks;
- Headgear;
- Work boots;
- And jackets to avoid exposure to low temperatures.
These are necessary to ensure safe working in any refrigerant or HVAC-eligible working environment.
4: Safe Handling and Storage Procedures
There are a lot of guidelines and rules about handling certain devices or equipment. These procedures are of a vast variety, and one example is how OSHA portable ladder safety tips have a separate set of guidelines of their own.
That’s why it’s not only necessary but quite important to ensure the regulation of safe handling and storage procedures. For instance, OSHA safety training can provide specific forklift safety tips by OSHA or other necessities for handling key areas in a refrigeration facility, etc.
5: Emergency Response Planning
Emergency response planning is one of the first things that OSHA inspectors check for when they inspect any workplace. How well is your workplace prepared to tackle any potential safety risks?
That’s why it’s important to figure out the right emergency response and seek the help of experts to put a plan in place if you don’t have one.
Conclusion
These are some of the top considerations to protect a team according to OSHA’s HVAC guidelines for refrigerant safety. It’s important to ensure regulation of these tactics, and of safety training to employees and supervisors. Only then can an employer keep their workplace safe and secure.