
In the manufacturing industry for 2022, smart manufacturing technology will continue to be at the forefront as companies explore innovative ways to improve processes and efficiency. 2021 brought upheaval and recovery, and 2022 brings smart manufacturing trends and technological applications you will want to understand.
As we explore these trends, we will be able to assist you in optimizing your operations and contributing to the health and resilience of your business.
Smart Manufacturing Trends for 2022
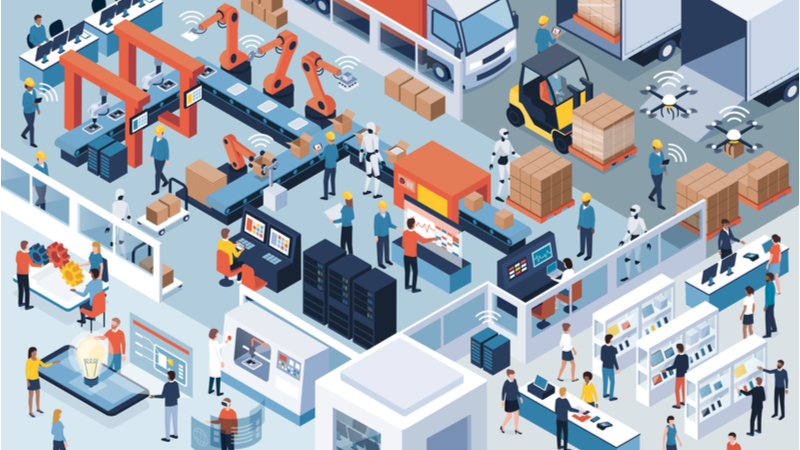
Certainly, 2022’s smart factory trends will be driven by recovery and preparedness, but they will also build on advancements in technology that date back decades – independent of the COVID pandemic and response. A few trends will be discussed below.
- Remote and off-site operational work is on the rise due to a number of reasons. Safety, flexibility, convenience — The list goes on and on. After the COVID scare, the world has returned to normal in a way, but facilities are closely monitoring ways to build even more remote access into their operations.
Monitoring sensors to virtual maintenance and troubleshooting through the Industrial Internet of Things and digital twins have proven that effective operations can still be conducted even when an employee isn’t present. This trend will only grow in the years to come as digital technologies become more prevalent. - Monitoring the health of machines with sensors: The use of sensors has been increasing in manufacturing for years. The year 2021 is poised for a critical mass breakthrough, with sensors becoming more popular at increasingly affordable prices.
More and more facilities will begin to use sensors to enable continuous, real-time monitoring of machine and equipment health and condition – resulting in more effective maintenance, longer equipment life, and higher-quality output. Increased productivity and efficiency thanks to sensors: Sensors allow for tactics such as predictive maintenance, which analyzes machine performance data to detect minor fluctuations in areas such as vibration, which can signal major issues later on – allowing the facility to address problems as soon as possible. In this way, downtime can be reduced or eliminated, allowing facilities to maximize productivity through proper equipment operation. - Taking a more predictive approach – beyond maintenance: In the wake of a global catastrophe, a more anticipatory approach to operations will be highly coveted. Companies in the manufacturing sector understandably aim to stay ahead of the next disruption, no matter when and wherever it occurs. Using AI and big data mining technologies will increasingly be used for running global scenarios to help predict and prepare for such events.
- AI exploration and adoption: Artificial intelligence is also poised for a breakthrough on the shop floor, taking advantage of years of incremental adoption as well as related technologies such as machine learning. AI technology can prove useful in managing maintenance, production capacity, inventory, sales, and many other aspects of a company’s operations.
- Personnel functions are changing – and there are opportunities to learn: In the future, AI will require skilled people to implement, manage, and make sense of the technology – a far cry from the fear that it will replace us. A boom in AI will provide manufacturing employees with great opportunities to learn and advance in their careers. Additionally, manufacturing personnel operations may change so that organizations can use technical workforce partners more effectively and maximize their value.
- Cobots on the rise: In the same vein, human workers remain an invaluable part of hands-on manufacturing tasks themselves, even if technology is increasingly used to facilitate them. Cobots (collaborative robots) is a suitable example of such an automation device – a machine with smart technology and safety features that makes it possible for it to work side by side with humans.
- Transparency and accountability have been driven by technology: As a result of the disruptions in 2020, smart technology will also affect the supply chain, and a high level of interest in reliability, transparency, and flexibility is expected.
A variety of technologies like artificial intelligence, vendor management software, and blockchain will play a role in the future of the supply chain – a process that can no longer be viewed as an intractable monolith, but rather a process that allows for more accountability and flexibility. - A new take on scenario planning: Smart technologies, like AI and big data, are providing managers and employees with a better understanding of potential future disruptions in the manufacturing industry. However, responses must still be planned to avoid these scenarios in the future.
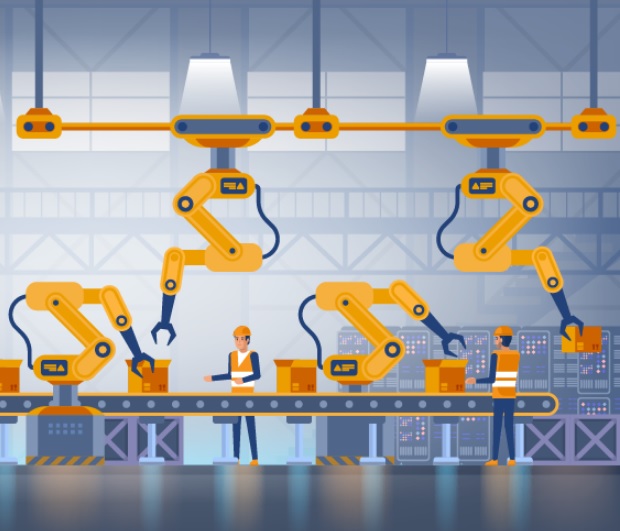
COVID has proven that long-term problems must also be addressed in addition to short-term responses to disasters. The planning exercises will consider agility, flexibility, resilience, employee relations, and long-term recovery in addition to immediate response planning.
Developing a reliable forecast of the future is impossible, as 2020 illustrates. The use of short-term trends, as well as long-term forecasts and focusing on the big picture (such as flexible production, reliability, remote work, maintenance partnerships, monitoring of equipment, and data-driven features), helps manufacturing businesses stay competitive and well-positioned.